產(chǎn)品列表
二輥開煉機的混煉效果與哪些因素有關(guān)
二輥開煉機的混煉效果主要與以下幾個因素有關(guān):
容量:每次混煉的膠料容積大小要依煉膠機的規(guī)格及膠料配方特性合理決定。容量過大會使輥距上方的堆積膠量過多而很難進輥距,使混煉分散效果下降,而且因散熱不佳會使混煉溫度升高,容易產(chǎn)生焦燒現(xiàn)象而影響膠料質(zhì)量。容量過大還會導(dǎo)致設(shè)備超負荷和勞動強度變大等一系列其他問題。容量過小會影響生產(chǎn)效率。
輥距:在合理的裝膠容量下輥距以4~8mm為宜。輥距過大,不利于配合劑的分散。輥距減小,膠料通過輥距時的剪切效果大會加快混合分散速度;但同時也增加生熱量,使堆積膠量增多,散熱困難,又影響剪切分散效果。所以,隨著配合劑不斷加入,膠料的容積變大,輥距也應(yīng)逐步調(diào)大,以保持輥距上方的堆積膠量適當(dāng)。
輥速與速比:提高輥筒的轉(zhuǎn)速和速比會增加混煉時對膠料的剪切作用與混合分散效果,但也會提高膠料混煉時的生熱升溫速度,易于焦燒,又影響剪切效果。輥速過快操作危險性也大,輥速和速比過小又會影響機械剪切分散效果和生產(chǎn)效率。所以開煉機混煉的輥筒轉(zhuǎn)速一般控制在16~18r/min。速比應(yīng)比塑煉時小,一般在1:(1.1~1.2)。合成橡膠混煉時的速比應(yīng)比天然橡膠上。
輥溫:開煉機混煉溫度就是輥筒表面的溫度,輥溫低,膠料的流動性差,生膠對配合劑粒子表面的濕潤作用下降,不利于混合吃粉,還會使設(shè)備負荷增加,若輥溫過低,膠料硬度太大,容易損壞設(shè)備;但可以提高機械剪切和混合分散效果。輥溫提高可以減少膠料的黏度,提高流動性和對配合劑粒子表面的濕潤性,加快混煉的吃粉速度。但若溫度過高容易產(chǎn)生膠料脫輥現(xiàn)象和焦燒現(xiàn)象,很難操作,也會影響對膠料的剪切分散效果和混煉質(zhì)量。故應(yīng)根據(jù)生膠種類和配方特點合理決定混煉溫度,并使輥溫控制在包輥性合理的溫度范圍以內(nèi)進行混煉。由于膠料在混煉過程中不斷生熱,應(yīng)及時加強冷卻調(diào)節(jié)輥溫,使之保持在適宜溫度范圍內(nèi)。另外,為了便于操作,開煉機混煉時前后輥溫度保持5~10℃溫差。由于天然橡膠容易包熱輥,因而前輥溫度應(yīng)高于后輥。多數(shù)合成膠容易包冷輥,故前輥溫度應(yīng)低于后輥。同時,因合成橡膠混煉時生量比天然橡膠多,故混煉時的兩輥溫度均應(yīng)比天然橡膠低5~10℃。
混煉時間:開煉機混煉時間受開煉機轉(zhuǎn)速和速比、容量和加藥順序、混煉的操作方法及混煉溫度、膠種和配方的影響,混煉時間短,配合劑分散不好,膠料質(zhì)量和性能差;混煉時間過長容易發(fā)生焦燒和過煉現(xiàn)象,也影響膠料質(zhì)量和性能,生產(chǎn)效率也低。適宜的混煉時間由試驗決定,并應(yīng)在混煉質(zhì)量的前提下盡可能縮短混煉時間,以提高生產(chǎn)效率和節(jié)約能耗?;鞜挄r間一般為20~30min,膠料可在40min以上,合成橡膠混煉時間約比天然橡膠長1/3左右。
加藥順序:配合劑的添加順序是影響開煉機混煉的重要的因素之一。加料順序不當(dāng)有可能造成配合劑分散,使混煉減慢,并有可能導(dǎo)致膠料出現(xiàn)焦燒和過煉現(xiàn)象,使混煉膠質(zhì)量下降,還會引起膠料發(fā)生脫輥現(xiàn)象而很難進行混煉操作。
以上六點就是影響二輥開煉機混煉效果的具體因素,在使用二輥開煉機時,要根據(jù)以上六點的具體情況進行操作,才能獲得適合的塑煉膠。
容量:每次混煉的膠料容積大小要依煉膠機的規(guī)格及膠料配方特性合理決定。容量過大會使輥距上方的堆積膠量過多而很難進輥距,使混煉分散效果下降,而且因散熱不佳會使混煉溫度升高,容易產(chǎn)生焦燒現(xiàn)象而影響膠料質(zhì)量。容量過大還會導(dǎo)致設(shè)備超負荷和勞動強度變大等一系列其他問題。容量過小會影響生產(chǎn)效率。
輥距:在合理的裝膠容量下輥距以4~8mm為宜。輥距過大,不利于配合劑的分散。輥距減小,膠料通過輥距時的剪切效果大會加快混合分散速度;但同時也增加生熱量,使堆積膠量增多,散熱困難,又影響剪切分散效果。所以,隨著配合劑不斷加入,膠料的容積變大,輥距也應(yīng)逐步調(diào)大,以保持輥距上方的堆積膠量適當(dāng)。
輥速與速比:提高輥筒的轉(zhuǎn)速和速比會增加混煉時對膠料的剪切作用與混合分散效果,但也會提高膠料混煉時的生熱升溫速度,易于焦燒,又影響剪切效果。輥速過快操作危險性也大,輥速和速比過小又會影響機械剪切分散效果和生產(chǎn)效率。所以開煉機混煉的輥筒轉(zhuǎn)速一般控制在16~18r/min。速比應(yīng)比塑煉時小,一般在1:(1.1~1.2)。合成橡膠混煉時的速比應(yīng)比天然橡膠上。
輥溫:開煉機混煉溫度就是輥筒表面的溫度,輥溫低,膠料的流動性差,生膠對配合劑粒子表面的濕潤作用下降,不利于混合吃粉,還會使設(shè)備負荷增加,若輥溫過低,膠料硬度太大,容易損壞設(shè)備;但可以提高機械剪切和混合分散效果。輥溫提高可以減少膠料的黏度,提高流動性和對配合劑粒子表面的濕潤性,加快混煉的吃粉速度。但若溫度過高容易產(chǎn)生膠料脫輥現(xiàn)象和焦燒現(xiàn)象,很難操作,也會影響對膠料的剪切分散效果和混煉質(zhì)量。故應(yīng)根據(jù)生膠種類和配方特點合理決定混煉溫度,并使輥溫控制在包輥性合理的溫度范圍以內(nèi)進行混煉。由于膠料在混煉過程中不斷生熱,應(yīng)及時加強冷卻調(diào)節(jié)輥溫,使之保持在適宜溫度范圍內(nèi)。另外,為了便于操作,開煉機混煉時前后輥溫度保持5~10℃溫差。由于天然橡膠容易包熱輥,因而前輥溫度應(yīng)高于后輥。多數(shù)合成膠容易包冷輥,故前輥溫度應(yīng)低于后輥。同時,因合成橡膠混煉時生量比天然橡膠多,故混煉時的兩輥溫度均應(yīng)比天然橡膠低5~10℃。
混煉時間:開煉機混煉時間受開煉機轉(zhuǎn)速和速比、容量和加藥順序、混煉的操作方法及混煉溫度、膠種和配方的影響,混煉時間短,配合劑分散不好,膠料質(zhì)量和性能差;混煉時間過長容易發(fā)生焦燒和過煉現(xiàn)象,也影響膠料質(zhì)量和性能,生產(chǎn)效率也低。適宜的混煉時間由試驗決定,并應(yīng)在混煉質(zhì)量的前提下盡可能縮短混煉時間,以提高生產(chǎn)效率和節(jié)約能耗?;鞜挄r間一般為20~30min,膠料可在40min以上,合成橡膠混煉時間約比天然橡膠長1/3左右。
加藥順序:配合劑的添加順序是影響開煉機混煉的重要的因素之一。加料順序不當(dāng)有可能造成配合劑分散,使混煉減慢,并有可能導(dǎo)致膠料出現(xiàn)焦燒和過煉現(xiàn)象,使混煉膠質(zhì)量下降,還會引起膠料發(fā)生脫輥現(xiàn)象而很難進行混煉操作。
以上六點就是影響二輥開煉機混煉效果的具體因素,在使用二輥開煉機時,要根據(jù)以上六點的具體情況進行操作,才能獲得適合的塑煉膠。
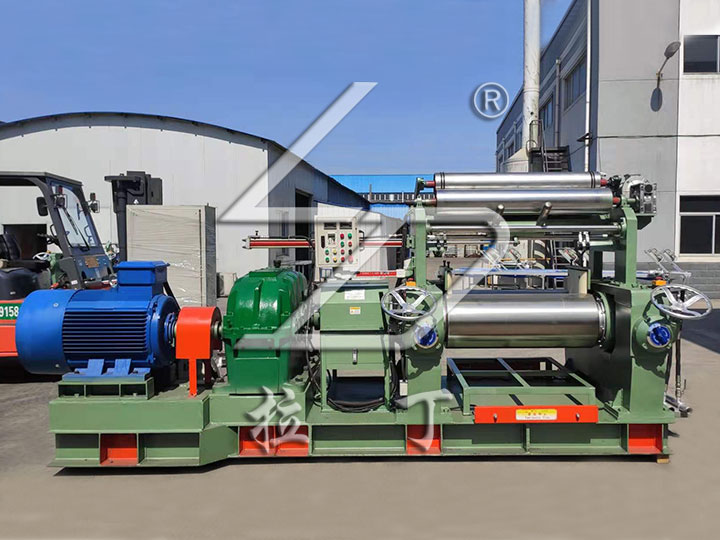